Find the whole guide to corrugated box design, including information on varieties, benefits, and creative applications. Now get professional advice and insights!
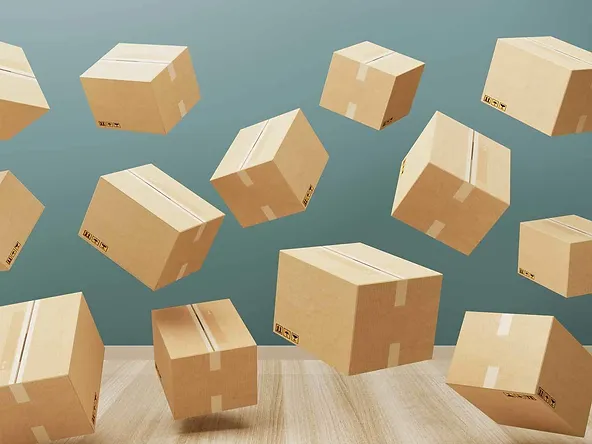
Corrugated Box Design is a procedure of aligning corrugated plastic or fiberboard (also known as corrugated cardboard) design elements with the functional, processing, and end-use requirements is known as corrugated box design. Packaging engineers strive to keep overall system costs under control while satisfying a box’s performance criteria. Corrugated boxes are shipping containers with significant functional and financial implications that are used for transport packing.
Printed bar codes, labels, and graphic design are essential in addition to the structural design covered in this article.
Uses Of Corrugated Box Design
One common usage for corrugated box design is as shipping containers. From product manufacture, to distribution, sale, and occasionally end-use, boxes must hold the product. While boxes can protect products to some extent on their own, they frequently need inside elements like blocking, bracing, and cushioning to help shield delicate contents. The specific logistics system in use determines a lot of the shipping risks. For instance, boxes sorted and delivered through a portion of their distribution cycle as mixed loads do not experience individual handling, whereas boxes unitized into a unit load on a pallet do or express carriers may be subjected to violent blows, strikes, and other actions.
Standard shipping containers need bar codes for routing, printing and labels to identify the contents, and legal and regulatory information. High-quality images are frequently employed in boxes for marketing, retailing, and point-of-sale purposes to assist convey the contents. Some boxes—referred to as “Retail Ready Packaging”—are made to be displayed with their contents facing down on the shelf. Some are intended to assist in dispensing the contents. Corrugated Box Design are mostly used for conveying various types of goods and are well-liked for their robustness, longevity, light weight, recyclability, and affordability.
Owing to the superiority and security of using corrugated box design to package goods, In the food sector, they are commonly utilized. Because the boxes can tolerate the strain that comes with stacking, they are ideal for convenient transportation.
Nearly 95% of all items shipped in the US are packaged in corrugated boxes. Corrugated paperboard makes up almost half of all recycled paper used in the US.
Stockpiling Strength Of Corrugated Box Design
A corrugated box’s ability to withstand crushing (product protection) and have sufficient strength for stacking in warehouses is one of its key features. It is necessary to give corrugated boxes more strength and moisture resistance if prolonged storage in high humidity is anticipated. Pallet loading technique has a big impact on stacking. The best box performance is achieved by vertical columns, while interlocking box layouts greatly degrade performance. It’s also crucial to consider how the pallets and boxes interact.
The grade of corrugated board, box design, flute direction, and inner supports can all be optimized while creating a box. Product support offers “load sharing” as well and can play a significant role. Box closures can occasionally affect how strongly boxes stack.
A regulated method of assessing boxes, stacks of boxes, and unit loads is box compression testing. The degree of control over stacking and dynamic compression field conditions is not the same. Based on container size, construction, and usage specifications, compression strength can be calculated; real package testing is frequently done to confirm these estimations.
Handling Power Of Corrugated Box Design
Numerous things are transported separately (in whole or in part) via mail, express carriers, or other mixed logistics systems. Boxes, box closures, and contents are subjected to extreme strain due to repeated physical handlings, computerized sorting, and uncontrolled stacking in trucks or air containers. Boxes intended for handling and storing unit loads might not be appropriate for mixed logistics systems. Corrugated shipping containers are subjected to additional stress during less-than-truckload transportation than during shipment by consistent pallet loads in trucks or intermodal containers.
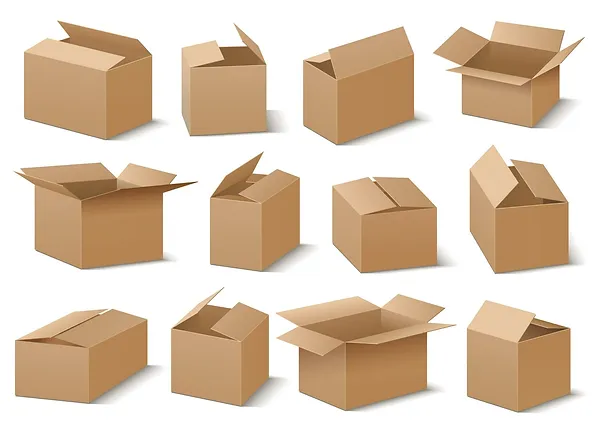
Sometimes the distribution system requires boxes to be built with a heavier construction. Testing of packages is frequently coordinated with anticipated shipping risks. This is reflected in the test protocols used by ASTM International and the International Safe Transit Association.
The number of messages provide instructions on how to create a box. There is advice on possibilities and things to think about in the Wiley Handbook of Packaging Technology. Recommended Materials and Box Structures for Specified Package Performance are covered in ASTM D5639 Standard Practice for Selection of Corrugated Fiber board Materials and Box Construction Based on Performance Requirements.
Certain corrugated box design require more stiffness or a heavier grade of board, depending on what’s inside. Hand holes and handles on boxes may require stronger boards, adhesively bonded reinforcing, or fibers imbedded in the board.
The Process Of Making Corrugated Box Design
A number of packaging messages go over things to think about when designing packages. The standards D6198, Standard Guide for Transport Packaging Design, and D5639 is produced by ASTM International. Standard Practice for Selection of Corrugated Fiberboard Materials and Box Construction Based on Performance Requirements. This point to several aspects that need to be considered, such as cost (materials, labor, capital), utility, performance of the package, machinability, marketing requirements, logistics considerations, risks related to transportation (compression, impact, rupture, humidity, condensation, temperature, pilferage), rules, and more.
The needs of the specific project come first for packaging engineers and designers. These needs include financial restraints, equipment capabilities, product attributes, logistical requirements, applicable laws, customer needs, etc. Computer Aided Design software coupled with automated sample-making tables is frequently used to create designs. Several possibilities for construction and a design could be taken into account
Samples are frequently sent to ASTM or other standard test protocols, such the International Safe Transit Association, for package testing. Graphic design complements structural design. Marketing staff occasionally employ focus groups or other quantitative methods to gauge acceptance of consumer-based designs. Test markets are utilized for significant programs.
Making corrugated board on a corrugating line, a lengthy network of connected devices that could be the size of an American football field is the first step in the process. When the single-wall corrugated board is finished, it consists of one corrugated layer positioned between two liners.
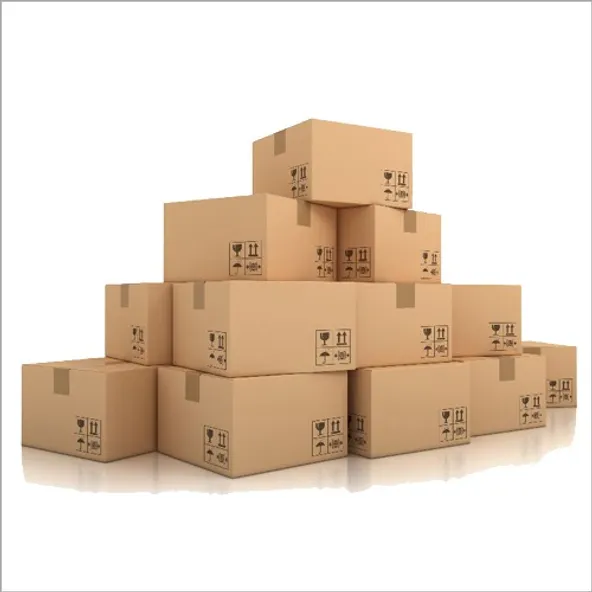
For every stack of box blanks, competent laborer’s create a job ticket and direct the blanks to the fabrication equipment. Rubber or tin sheets that are large and flexible are used to prepare printing dies and patterns. The box blanks are fed through them after they are loaded onto rollers and are then cut, scored, folded, and glued to produce a box. After being stacked, completed boxes are fed through a banding machine to be packaged and dispatched.
How To Design Corrugated Box
When it comes to stepping into the Corrugated Box Design , The Regular Slotted Container (RSC) is the most widely used box design. From score to edge, every flap has the same length. Unless the width and length are equal, the large flaps usually meet in the middle, whereas the minor flaps do not. A box’s dimensions might be measured externally for palletizing or handling machinery, or internally for product fit.
The manufacturer’s joint can be taped or stitched, although glue is typically used to link them. The packager receives the box flat, or knocked down, and assembles, packs, and seals it ready for delivery. Box closure methods include strapping, glue, tape, and staples.
Usually, internal dimensions are used to specify and order boxes. The European Federation of Corrugated Board Manufacturers (FEFCO) normally assigns a 4-digit designation to each box style; an RSC’s code is 0201.
How Corrugated Box Design Can Carry Dangerous and Hazardous goods
Corrugated Box Design is created with preventions , And Hazardous material and products shipment is strictly monitored. Every nation has standardized design and performance standards for shipments based on the UN Recommendations on the Transport of Dangerous Goods model legislation. Title 49 of the Code of Federal Regulations, for instance, contains rules released by the US Department of Transportation.
4G standards include a description of corrugated Box Design. Certification of performance (such as a severe drop test) is required for the box and its contents.
Corrugated Box Design : Box Closure
A box’s ability to close is a crucial component of Corrugated Box design. Production line equipment types, field performance, evaluated laboratory performance, and end users’ ease of use and safety when opening boxes all have an impact.
Conclusion
Finally, the guide on corrugated box design provides a thorough grasp of its applications and nuances. This comprehensive book provides both professionals and fans with invaluable insights, covering everything from examining different box kinds to investigating structural aspects and practical considerations.
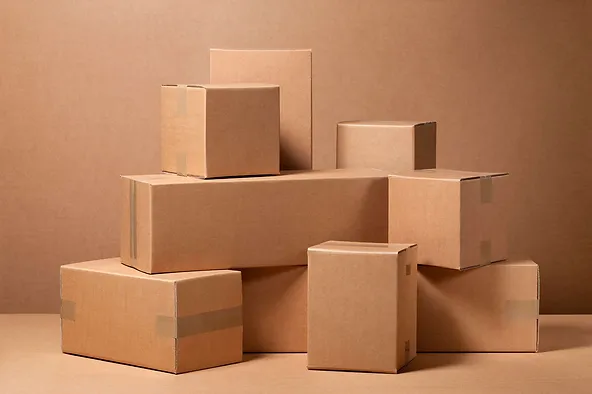
How is the strength of a corrugated box increased?
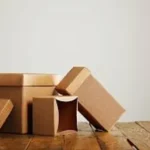
The more plies that surround the corrugated cardboard sheets that are made, the stronger the corrugated cardboard material will be. You can even add more plies to either side of the cardboard to make it stronger.
Which adhesive adheres to corrugated boxes the best?
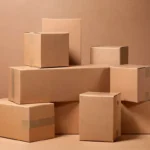
The ideal glue to use for corrugated cardboard cargo boxes is a starch-type glue. This glue, also known as vegetable glue, is safe for the environment since it is made of natural polymers that are present in the seeds and roots of many different plants, including maize.
How is a corrugated box’s thickness measured?
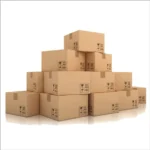
To perform this calculation, measure the box’s outside, multiply the length by the width by the height, then divide the result by 166. When measuring, fractions are rounded to the nearest inch.